
With today’s consumer focus on “farm to table,” retailers are being pushed to supply local foods, especially in produce — giving rise to new opportunities for small growers. But because those same retailers also are being pushed by both consumers and regulators to increase their food safety standards and transparency, the opportunities come with increased responsibility for traceability to the root, regardless of grower size.
Whether the produce is grown in a greenhouse, a one-acre plot, or an expansive field, it needs to be able to be traced back from table to farm. “Pathogens don’t care about size; they’re not selective,” said United Fresh Produce Association (UFPA) vice president of supply chain management Dan Vaché. E. coli-contaminated leafy greens from a small farm are no different than E. coli-contaminated leafy greens from a large farm except in the number of people potentially sickened or even killed. “If everyone doesn’t follow food safety practices, it’s detrimental to everyone, including customers,” Vaché said.
But having a traceability system doesn’t just enable a specific lot of contaminated produce to be accurately determined, it enables non-contaminated lots to be ruled out, limiting the amount requiring recall or disposal, and enabling a retailer to say it deals with suppliers that are not involved in the recall. It is for all these reasons that all growers, large or small, need to have a traceability system.
Produce Traceability Initiative
It also is for all those reasons that the UFPA, Canadian Produce Marketing Association, and Produce Marketing Association formed the Produce Traceability Initiative (PTI) in 2007. It all started with the 2006 multistate outbreak of E. coli infections linked to fresh spinach from California, which sickened more than 200 people in 26 states and caused at least three deaths.
“It was a wake-up call,” Vaché said. “It took over six weeks to figure out the trace-back/trace-forward, and that literally killed the spinach market.” Even though there was unimplicated, viable spinach being grown in the Eastern U.S., there was no confidence that the industry knew where the contaminated spinach was from, so spinach was avoided altogether. Even CDC advised, “If consumers cannot tell if a brand of fresh spinach was implicated in the outbreak and the package has a ‘use-by date’ of October 1, 2006, or earlier, they should not eat it.”

“As an industry, we said we need to do a better job,” Vaché said. “How do we link beyond one forward/one back? How do we figure out where it came from — quickly?” So the industry came together to create PTI, a voluntary, industry-wide effort designed to help produce companies and their buyer partners move toward achieving whole-chain traceability. The initiative is based on the GS1 System standards, that is, the barcode seen on nearly every item put up for sale.
While FDA does not endorse specific processes, Vaché said the agency gave a nod to PTI because it fulfilled FDA’s criteria: It had a common language, it tracked by lot number and its electronic recordkeeping enabled traceback within 24 to 48 hours. So the next step was to provide information on implementing PTI, for which it developed a seven-milestone checklist:
- Brand owner obtains company prefix.
- Assigns 14-digit GTIN number to every case configuration.
- Provides GTIN information to buyers.
- Packer provides and shows human readable information on each case.
- Packer encodes information in GTIN barcode, lot number.
- Each subsequent handler reads and stores GTIN and lot number from each case of produce received, so information is retained for traceback.
- Each subsequent handler reads and stores information on outbound cases. (For detailed information on each step, see 7 Milestones to PTI Implementation, bit.ly/2oFWA9o).
Additionally, understanding that the
food industry is a low-margin industry, Vaché said, “There are solutions and it doesn’t have to be expensive. There are ways to do it even for those working with small margins.”
A free software
One of those ways is that developed by eHarvestHub CEO and cofounder Alvaro Ramirez, who said, “I thought it was great that industry came up with its own standard, and I saw PTI as a tool that enables small to mid-size growers to be at the same level as the bigger growers.” But, he added, “I saw that it was an expensive technology for small farmers.”
So, Ramirez made the decision to create a software tool that would provide a simple way for small growers to implement PTI — and offer it for free. “At the end of the day, PTI reduces financial risk for all,” he said.
Of course, no business can operate without some income, so “where we make money is in helping to market the product,” Ramirez said. Once input, the data is stored in an online system which retailers and foodservice companies can access to search for and order available produce, combining sources as needed to meet its needs. The produce is then transported by approved contract truckers. This direct link to buyers and all transactions remaining within the online system enables growers to easily implement PTI traceability from farm to retail, along with an inventory management system.
The system is also flexible enough to ensure it can be adapted to meet FSMA traceability rules once those are finalized, Ramirez said. “But, bottom line, it’s all about recordkeeping. There are a lot of custom technologies in business; we were trying to find a standard.” Not only was PTI just what the company was looking for, the use of the standard as the basis of its eHarvestHub technology has won the company 14 awards, he said.
Evolutionary growth
PTI has been in existence for a decade, and about 50 to 60 percent of produce growers are compliant, but retailers are not all using it yet, Vaché said. However, he added, as they start realizing its additional unintended positive consequences, large retailers are beginning to buy in.
By checking the actual harvest dates of different shipments that come in on the same day, a retailer can ensure it is working in real-time first in/first out based on actual harvesting of the crop. Another aspect being implemented by a Mexican grower is that of putting pictures of the person who picked each tomato on the label. As such, Vaché said, “PTI continues to move forward … unfortunately, it’s at glacial speed.”
To get the most out of any traceability system, growers and retailers need to consider how it can provide additional benefits. “Yes, it's about traceability, but think how it can improve your other operations,” he said. “There is an investment to be made, but it’s an investment in your business.”
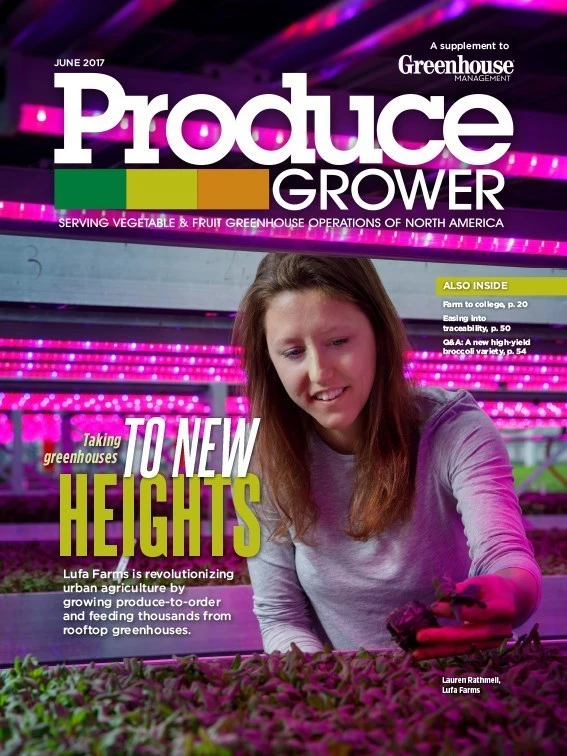
Explore the June 2017 Issue
Check out more from this issue and find your next story to read.
Latest from Produce Grower
- University of Evansville launches 'We Grow Aces!' to tackle food insecurity with anu, eko Solutions
- LettUs Grow, KG Systems partner on Advanced Aeroponics technology
- Find out what's in FMI's Power of Produce 2025 report
- The Growth Industry Episode 3: Across the Pond with Neville Stein
- The Growth Industry Episode 2: Emily Showalter on how Willoway Nurseries transformed its business
- 80 Acres Farms expands to Georgia, Texas and Colorado
- How BrightFarms quadrupled capacity in six months
- Oasis Grower Solutions releases two foam AeroSubstrates for hydroponic growers