
Even when ongoing, routine cleaning and sanitation is conducted during the greenhouse growing seasons, problems can develop and build in out-of-the-way, hidden and hard-to-reach areas. For that reason, treating the time between growing cycles as an opportunity to create a “clean stop” can help reduce contamination in your greenhouse and keep your produce healthier.
In fact, Sunset Grown vice president of food safety & quality Joe Darden sees the most critical aspects of sanitation in greenhouse produce growing as being effective cleaning and sanitation at crop stop and cleanout. “This is critical to mitigate transfer of food or plant pathogens, plant viruses or insect eggs or larvae to the next crop cycle,” Darden says. While the extent of the potential for such contamination depends on the current crop’s micro, viral or pest pressure, “one can easily make a big mess of things when not properly cleaned/sanitized — leading to a disaster crop the next crop cycle,” he says.
Cleaning vs. sanitation When preparing to create a clean stop between cycles, it is important that the differences between cleaning and sanitation be understood. They are not the same thing.
As defined by FDA:
- Cleaning is the process of washing, rinsing and visually inspecting food or food-contact surfaces to eliminate dust, dirt, food residues and other debris.
- Sanitizing is the application of a process — to a cleaned surface — that is effective in destroying vegetative cells of microorganisms of public health significance and substantially reducing numbers of other undesirable microorganisms, without adversely affecting the product or its safety for the consumer.
- In brief, you clean to remove soils and debris and sanitize to reduce microorganisms.
Thus, implementing cleaning and sanitation to produce a sanitary environment involves seven general steps:
One can easily make a big mess of things when not properly cleaned/sanitized — leading to a disaster crop the next crop cycle.” — Joe Darden, vice president of food safety & quality at Sunset Grown
- Inspection. A visual assessment of the greenhouse is a good first step, as it will enable you to better schedule the cleaning and sanitation actions that will be needed, and have all the necessary equipment on hand.
- Tools, benches and equipment. When possible and feasible, benches, tables, tools and equipment should be moved, or at least pulled away from walls and each other to enable access to all areas. Breaking down equipment for cleaning and sanitizing will allow you to get into cracks and crevices where pests and pathogens can harbor. Weed mats should be removed and replaced as needed, particularly to limit cross-contamination from a previous pathogenic outbreak.
- Cleaning. In addition to the physical sweeping and wiping of surfaces to remove visible residue and debris, Michigan State University recommends that growers consider power washing the concrete pathways, walls, benches and other equipment of the greenhouse to remove dirt, algae and other sources of pathogens. Cleaning also would include the removal of weeds that escaped weed mats or are under the benches, and the replacing of plastic.
- Rinsing. Before moving on to a sanitation step, any surfaces on which cleaning product has been used should be completely rinsed. Rinsing also can help remove any small debris or soil that may have been missed.
- Sanitizing. Heat and chemicals are the two most common forms of sanitizing, and in the greenhouse, this should include all food-contact surfaces, but could involve everything from walls and floors to work tables and benches to equipment and re-usable pots. In general, heat sanitation will be a function of steam, hot water or hot air. For chemical sanitizers, Clemson University recommends the consideration of three factors: concentration — too little can be ineffective and too much can be toxic; temperature — chemical sanitizers generally work best when mixed in water that is 55 to 120° F; contact time — a specified length of time will be needed to ensure effective cleaning. In all cases, the label directions must be thoroughly read and followed.
- Rinse/Air dry. As with cleaning, all surfaces need to be rinsed with clean water and left to dry.
- Validation. Once completed, the cleanliness of the surfaces — particularly those likely to have any direct contact with the produce, should be tested to ensure the effectiveness of the cleaning and sanitation processes.
Though not technically a part of the process, an eighth step would be to keep the environment clean through to the next crop cycle to guard against cross-contamination and ensure the biosecurity of the new crop. Following sanitation, Darden says, it is critical to avoid introducing harmful food or plant pathogens, plant viruses or diseases, harmful insects or rodents through sloppy footwear cleaning, leaving open doors and vents, allowing uncontrolled visitors (people/neighbors) in your crop, not cleaning/sanitizing new equipment or replacement equipment or equipment that has been temporarily stored outside before being re-introduced to the sanitized facility, etc. This is, in fact, an area of sanitary concern that a grower can easily miss or not think to address.
While it may seem that it is best to hold off on cleaning and sanitation until a week or so before the new cycle, growers should plan to conduct at least the cleaning steps as soon as possible. Doing so acts as a preventive step — to help to immediately reduce pest and pathogen harborage, thus decreasing the potential for population growth during the down time, and reducing the need for pesticides or other reactive applications.
Get curated news on YOUR industry.
Enter your email to receive our newsletters.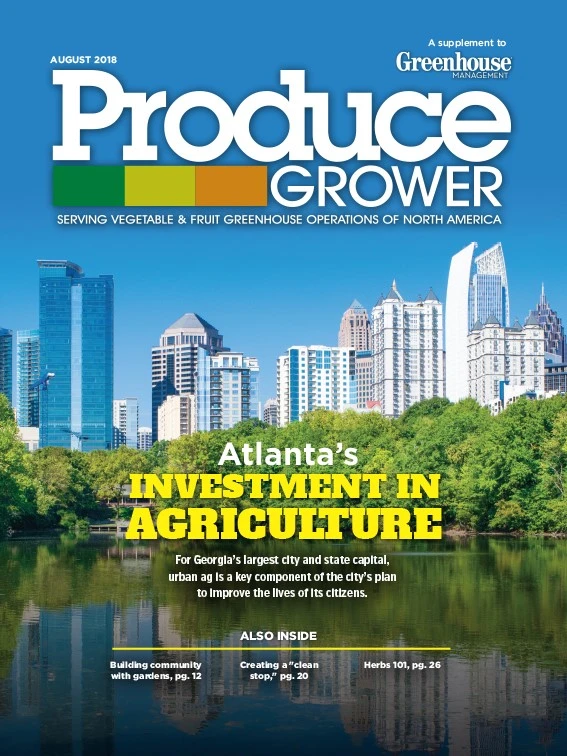
Explore the August 2018 Issue
Check out more from this issue and find your next story to read.
Latest from Produce Grower
- The Growth Industry Episode 3: Across the Pond with Neville Stein
- PG CEA HERB Part 2: Analyzing basil nutrient disorders
- University of Evansville launches 'We Grow Aces!' to tackle food insecurity with anu, eko Solutions
- LettUs Grow, KG Systems partner on Advanced Aeroponics technology
- Find out what's in FMI's Power of Produce 2025 report
- The Growth Industry Episode 2: Emily Showalter on how Willoway Nurseries transformed its business
- 80 Acres Farms expands to Georgia, Texas and Colorado
- How BrightFarms quadrupled capacity in six months