
Integrated technology is improving for the produce market. Picture produce moving along a conveyor belt, then being picked up by delicate and adaptive robotic handles and cut with a 50,000-PSI waterjet. Together, these specialized parts constitute Heinzen Manufacturing International’s new Automated Produce Cutting System.
This system processes multiple types of produce, says Rudi Groppe, Heinzen president and CEO. “Anywhere that you’re picking and pulling and moving, this technology could [be applied],” he says.

How it works
Heinzen is the integrator of the technology, says Heinzen sales engineer Willi Ortner. The company partnered with Yaskawa Motoman, which developed the wash-down duty robot; Soft Robotics, which developed the gripper technology and end-of-arm-tooling; and KMT Waterjet Systems, which developed the waterjet.
The system’s individual components are highly specialized. In addition to its 50,000-PSI waterjet that cuts the produce, its soft robotic handles are adaptive enough to securely grab and hold fruits and vegetables and conform to the unique shapes of individual pieces.
The Automated Produce Cutting System replaces two to three employees and has a target return on investment of a year to 18 months, Ortner says. It is typically an investment for processors, but growers could use it themselves as an added step.
Recent improvements in robotics
In recent years, robotics manufacturers developing tech for produce operations have taken several steps to improve their technologies. One of the first issues the produce industry had to face was manufacturing of the soft robotics gripper, Groppe says. “You can fine-tune the design of it and the force of it, so you can actually pick up tomatoes, strawberries [and] apple wedges without any mechanical damage,” he says. “That was the first step in [replacing] some of the steps that a human does.”
Another major development was in camera technology, Groppe says. With nearly every robotic manufacturer recognizing and processing images, and more of them using a process called blob detection, an increasing number of them can integrate.

Then comes conveyance. Current systems can now run mini sweet peppers along a conveyor belt, pick them up and cut the buds off them, Groppe says. “That’s an operation now that with the gripping technology, the camera technology and conveyance, you can actually automate it, where five years ago, that was pretty much always going to be 40 people in front of a conveyor belt, picking up each product, hand-orienting and placing it,” he says.
Robotics manufacturers are consistently trying to determine how to speed up multiple steps that humans currently perform, Groppe says. In the case of strawberries, workers inspect the quality of fruit, cut them and put them on another conveyor for sorting.
What does this mean for growers and processors? “Part of the robotic solution is not replacing labor 100 percent,” Groppe says. “It’s just extending what one worker can do by four, five, six times the productivity rate of that individual.”
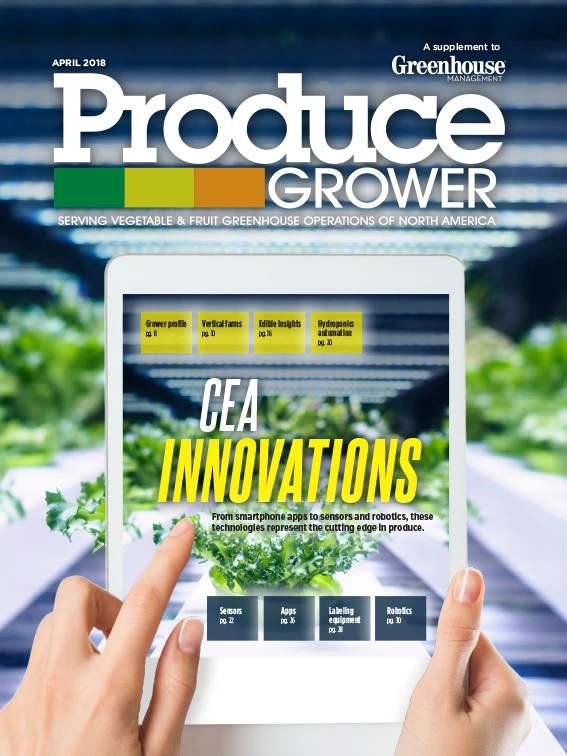
Explore the April 2018 Issue
Check out more from this issue and find your next story to read.
Latest from Produce Grower
- University of Evansville launches 'We Grow Aces!' to tackle food insecurity with anu, eko Solutions
- Lawsuit challenges new H-2 visa rules
- Q&A: Sandra Eskin Leads Food Safety Advocacy Organization, STOP, as CEO
- Find out what's in FMI's Power of Produce 2025 report
- The Growth Industry Episode 3: Across the Pond with Neville Stein
- Martin A. Makary Sworn in as FDA Commissioner
- PG CEA HERB Part 2: Analyzing basil nutrient disorders
- LettUs Grow, KG Systems partner on Advanced Aeroponics technology