
In the February issue, we introduced you to Brian Lynch, the new director of horticultural technology solutions at Vineland Research and Innovation Centre (Vineland) in Ontario, Canada. Vineland has identified six main challenges facing horticultural automation development. If you missed it, read it here: bit.ly/Vineland-Lynch.
As labor availability and costs continue to afflict the ornamental industry, growers dream of automated solutions for production tasks. Last fall in the Greenhouse Management State of the Industry survey, 55% of respondents said they’d like to automate more tasks and 19% said they’ve adopted automation to help combat labor shortages.
Let’s take a look at three technologies – two that have been deployed and one that is close to being released – that are applicable to ornamental production.

‘Spyder’ senses
Elmar Mair, co-founder of Neatleaf, developed a technology that is running in cannabis operations, but, he says, is applicable now to ornamental growers. The Neatleaf Spyder is a cable-based robot that operates above the plant canopy and is equipped with several sensors. The sensors are designed to gather a comprehensive understanding of the growing environment.
The Spyder and its sensors identify plant stress multiple times per day, and the dashboard provides a full zone view or the ability to take a closer look at a group of plants or even an individual plant. It collects data points such as temperature, humidity, CO2, plant height and leaf temperature. It can also measure light conditions. “It moves around the whole space all the time and is out of the way,” Mair explains. “It collects the data and provides a full overview of your canopy multiple times a day.”
With the use of AI, the Spyder identifies plant stress such as leaf yellowing, chlorosis, leaf damage, powdery mildew or pest damage. It summarizes conditions and trends, then points the user to the problems.
“Besides identifying plant stress before a grower sees it, this technology can help growers go back in time and see when that stress started, how it evolved and how it spread,” Mair says. “Everything is quantified and put into numbers. You can compare the data with other growth cycles, and you get this immediate feedback loop. [This technology] can take over the burden of monitoring your crop, so that [growers] can focus on actually use their time to deal with the issues rather than spending so much time identifying them. It’s a huge labor savings. I think it’s going to really change how you can operate because you have this immediate feedback loop.”
With machine learning, the more data collected, the better the system gets, he adds.
Mair is convinced this technology is prime for ornamental use.
“This may be controlled environment agriculture, but we still have 10 to 20% crop loss depending on the crop. So it’s not really fully controlled and growers can’t measure and assess everything on their own. I think there’s a huge potential for us to actually bring those 10 to 20% losses down to a couple percent.”
Besides machine learning, Neatleaf also employs a plant science team who assesses the data and provides insights on how to use the system.
Mair is conducting experiments for the next generation of Neatleaf, which includes working with other sensors in the plant canopy, such as substrate, EC and pH sensors to integrate into the system. He also envisions a system with spray nozzles for pesticide and fungicide application, as well as the ability to snap pictures of sticky traps to analyze the pests in the greenhouse.


Precision harvesting
A gerbera harvesting robot was developed by researchers from the Agro Food Robotics program and the business unit Greenhouse Horticulture of Wageningen University & Research. The research project is a public-private partnership and is financed by the Gerbera Crop Cooperative and the Horticulture & Propagation Materials Top Sector.
A top view camera detects the flowers that are ripe and need to be harvested. A robot arm with an end-effector approaches the stem directly under the flower and descends to the bottom of the plant. Then the actual harvesting starts. There are roughly two methods for this: picking the stem or cutting the stem. The latter method has been chosen for the gerbera harvesting robot. The main advantage of this method is that the harvesting direction does not matter, which is the case with picking.
According to developers, the gerbera harvesting robot “has improved significantly.” The end-effector (which harvests the gerbera stems) “is considerably faster than before.” This is mainly thanks to changes in the way the gripper descends down the stem. In addition, the robot relies less on 3D visualizations, so the processing power needed to harvest the gerberas is shortened.
To harvest, the robot has to find the exact location of the stem. In the previous prototype, the robot calculated the position and orientation of the entire stem under the flower with the help of camera information and calculated 3D visualizations. This requires a lot of computing power, and time.
“In the new set-up, the robot does not use 3D images to calculate the stem position anymore. Instead, it locates the flower position, which is much easier to see. Then the robot arm descends to about 4 centimeters below the flower. That is logically the only place the stem can be and thus the highest chance the gripper can catch the stem. This method is significantly faster,” says Jos Ruizendaal, researcher and project lead.
It is not yet known when the robot will be on the market.
For more: bit.ly/vision-robotics
Autonomous help
Hippo Harvest in Pescadero, California, recently integrated autonomous mobile robots (AMRs) from Zebra to grow greens, enabling the company to save up to 92% of water and use 55% less fertilizer than conventional produce growers. Hippo Harvest is using advanced plant science, machine learning and robotics to grow leafy greens and other produce in sustainable greenhouse environments.
Hippo Harvest built a system that uses machine learning to determine how much water, fertilizer, and light is needed to produce its crops. Inside its greenhouses, Hippo Harvest is leveraging Zebra’s Freight100 AMRs to farm its plants more efficiently, from delivering precise levels of water and nutrition to plants to delicately harvesting the company’s crops. In addition, Zebra’s Fetch AMRs are assigned picking and moving tasks around its greenhouse facilities so workers can focus on more strategic activities. The AMRs also serve as a direct link for data collection for the company’s machine-learning algorithms to make improvements in production and greenhouse throughput.
“We found exactly what we needed with Zebra’s AMRs to develop growing methods that address some of the biggest challenges facing our food supply and the agriculture sector,” says Hippo Harvest CEO Eitan Marder-Eppstein. “We’re excited to continue collaborating with Zebra Technologies as we work to develop transformative growing processes that are sustainable and make the best use of our natural resources.”
Hippo Harvest signed The Climate Pledge, a commitment founded by Amazon and Global Optimism for businesses to reach net-zero carbon by 2040.
“Hippo Harvest has deployed Zebra’s AMRs inside its greenhouses to help farm plants more efficiently, save water and reduce food waste,” says Matthew Wicks, senior director of product management at Zebra Technologies. “Our robots are easy to configure and deploy, which allows for a variety of applications from repetitive pick and move to more complex activities such as harvesting of plants and data collection. We’re excited to help Hippo Harvest apply Zebra’s most advanced technology solutions to work in new ways and deliver fresh, sustainably grown produce to its customers.”
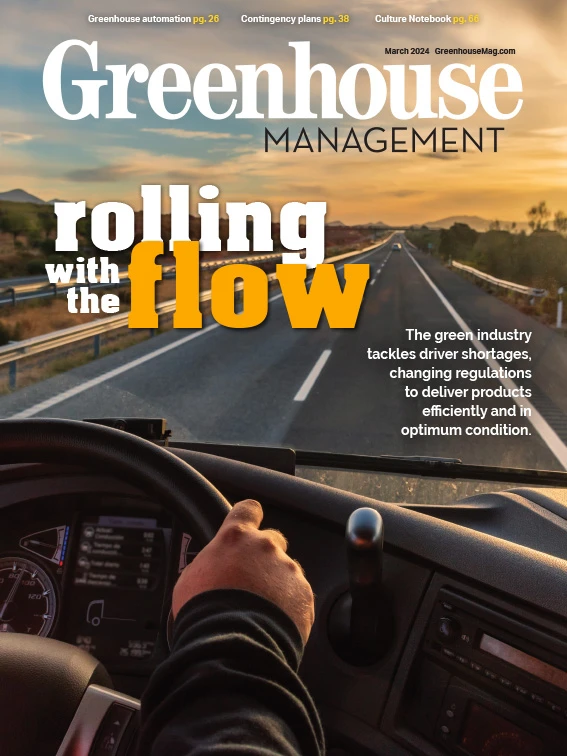
Explore the March 2024 Issue
Check out more from this issue and find your next story to read.
Latest from Produce Grower
- Sanitation station
- BioTherm launches Ultimate Grower Climate Control System
- FDA Finalizes Updated ‘Healthy’ Nutrient Content Claim
- Honesty is the best policy
- Happy holidays from the GIE Media Horticulture Group!
- Invest in silver
- VIDEO: Growing media for strawberries grown under different production systems
- Building the ‘Dream Greenhouse’