
As the cost of labor continues to rise and immigration issues cause uncertainty in the green industry, growers keep searching for ways to carry out the functions in a greenhouse as efficiently and as cost effectively as possible.
One area growers can look to improve efficiencies is in harvesting. This can mean anything from keeping blades sharp to making a significant investment in an automated harvester, such as a robot that picks the strawberries in your hoophouse. It also means constantly looking ahead and thinking out of the box to find more efficient ways to carry out this task.
Here is a look at some conventional harvesting equipment as well as some new innovations and timely thoughts on harvesting under cover.

Traditional harvesting tools
Nate Storey of Bright Agrotech, a manufacturer of vertical growing systems for greenhouses, suggests three different items for making harvesting as easy as possible. He says every grower should have a harvesting knife, which can be purchased for about $15. A harvesting knife has a nice, large handle and broad blade, perfect for cutting greens. He says garden shears, which come in every shape and size to suit the user, are also essential.
Johnson gathers the crop he is cutting into a lightweight, nonporous plastic crate. He says the nonporous crates reduce the chance of trapping harmful pathogens like you might in a wooden or cardboard box.
A new tool by Johnny’s Selected Seeds called the Greens Harvester is designed to harvest wide rows of leafy greens, like lettuce and arugula. Pete Johnson of Pete’s Greens in Craftsbury, Vt., harvests and sells about 1,000 pounds of salad greens per week. The greens are densely planted in 36-inch wide beds.

Last fall, Johnson used a prototype of the Greens Harvester for about six weeks. He says that at first it felt awkward to squat and move down the row with the manual harvester, but eventually it became second nature. He says keeping the blade “impeccably sharp” is the key to an efficient harvest with the new tool. Johnson carries a rag with him and stops every five to 10 minutes to clean and file the blade down with a diamond file.
“I’ve experimented with several other mechanical harvesting tools in the past,” says Johnson. “But the Greens Harvester is the first one that combines these benefits: It improves greens quality over knife harvesting (no squeezing of the greens), reduces harvest time, is simple and inexpensive, and is extremely portable.”
He says after some practice he was able to cut 200 pounds of greens per hour compared to about 25 pounds per hour with a harvesting knife. The Greens Harvester comes in three sizes: 32-inch, 42-inch and 48-inch, and sells for $249.

Traditional tools: keep them sharp
Keeping the tools sharp will keep the crew harvesting in the most efficient manner. There are some good options available for the task, including an automated sharpener, called the Work Sharp WSKTS Knife and Tool Sharpener. This power-driven tool uses fine, medium and coarse abrasive belts to sharpen a wide range of tools, scissors, etc., and sells for about $75. And of course, there are the less-expensive diamond type files, including fine and coarse diamond hones sold by various garden supply companies.
Robotics: wave of the future?
More than 30 percent of the total production costs in a greenhouse can be attributed to labor, according to an article by Wageningen UR. This is prompting companies to experiment with robotic harvesting equipment. One company that is trialing robotic harvesting equipment for covered growing systems in the U.S. is Agrobot. The company is headquartered in Huelva, Spain with an office in Oxnard, Calif.
The Agrobot SW 6010 Strawberry Harvester employs robotic manipulators with 60 robotic arms that are able to locate and identify plump, ripe strawberries and move them to the packaging area via their FlexConveyor System. The cost? Expect to pay about $250,000. The unit cost is weighed against the current costs of labor.
Looking ahead
Harvest Automation, out of North Billerica, Mass., doesn’t manufacture greenhouse harvesting equipment, per se, but rather a machine to move pots in and outside of a greenhouse. The HV-100 has been used by ornamental greenhouse growers, but may have applications for harvesting in a produce greenhouse. The machine can move containers from one location to another where they could be harvested more efficiently.
The company is currently experimenting in the outdoor environment in which containers can be moved from the ground where people would spend hours stooping and bending to harvest, up to a table where they could be harvested much easier and more efficiently. This could be done in covered structures where a crop, such as strawberries, is also being grown in the ground.
Harvest Automation’s CEO John Kawola understands the economics of greenhouse crop production and says growers need to increase the scale of their operation and/or find ways to reduce labor costs.
“I think the local, fresh, low-carbon footprint movement is fantastic,” says Kawola. “However, you’re going to need more automation — scale it up, use technology or both.”
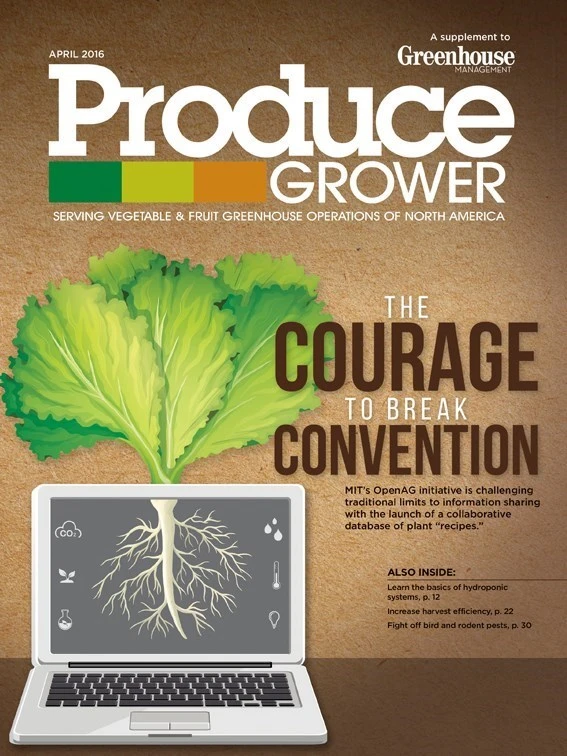
Explore the April 2016 Issue
Check out more from this issue and find your next story to read.
Latest from Produce Grower
- Your comprehensive guide to Indoor Ag-Con ’25
- Sollum Technologies and Indoor Ag-Con announce recipients of Sollum Student Scholarship
- 80 Acres Farms expands to Georgia, Texas and Colorado
- This fast and agile robotic insect could someday aid in mechanical pollination
- AmericanHort urges exclusion of sphagnum peat moss from proposed Canadian tariff
- The Growth Industry Episode 2: Emily Showalter on how Willoway Nurseries transformed its business
- Moleaer expands irrigation product line featuring nanobubble technology
- Eden Green Technology CEO Eddy Badrina reflects on challenges, opportunities for CEA