
Packhouses stick produce with labels that contain information such as barcodes, price look-up (PLU) numbers, brand and country of origin. With some packhouses labeling up to a billion fruits and vegetables a year, that’s a lot of labeling.
Founded in 1982, Sinclair Systems International focuses on automating the produce labeling process to improve efficiencies, says product manager Barry Lawson. The company’s systems label apples, citrus, kiwis, potatoes and avocadoes, as well as greenhouse-grown crops such as tomatoes, cucumbers and peppers. “If you go into a market today, it’s probably safe to say that 75 percent of the fruit in there has been labeled with Sinclair equipment,” Lawson says.
For years, Sinclair has pre-printed labels, working with an in-house graphic artist to create labels that are specific shapes and sizes, and match clients’ branding goals, Lawson says. But as packhouses wanted to increase productivity and decrease labor costs, they looked to more fully automated labeling technology.
Retailers request that 90 to 95 percent of their produce is labeled so they don’t lose revenue. If a piece of fruit doesn’t have a label on it, Lawson says a cashier could ring it up for a lower price than what it is worth. If a fruit is worth 50 cents and the cashier rings it up for 25 cents, that’s 25 cents gone. “The supermarket lost that revenue, the grower lost that revenue and the packhouse is going to lose that revenue as well,” he says.
Various systems from Sinclair, including direct thermal technology, online labeling and pattern labeling, have been replacing costly and imperfect labor in packhouses, Lawson says.

Direct thermal labeling
When running labels through Sinclair’s direct thermal technology machines, packers install bitmaps (images consisting of small dots) into the machine’s computer system. “You have fixed print on the label that we’ve made, so you’re going to have the brand name at the top and maybe something at the bottom, but at the middle, you want a different origin, PLU or [variable],” Lawson says.
When it comes time to label another type of produce, the operator picks out a new bitmap, but doesn’t have to change the cassette of labels, Lawson says.
Online labeling
In Sinclair’s online labeling systems, produce runs through a sizer to be measured for size, texture and bruising. The sizer recognizes the produce and sends a signal to the machine.
An example of an online labeling system is Sinclair’s six-head RM6 system, Lawson says. “You have lanes running across that can label all the fruit simultaneously,” he says. “Then we have a V6, which is a smaller, single-lane system that gives you some flexibility for smaller pack houses. If you want to unhook it and move it somewhere else, you have that luxury.”
Pattern labeling
Pattern labeling is popular in Europe, where produce is stacked on trays on top of each other at retail, Lawson says. In pattern labeling, trays that hold a certain amount of produce feed through a machine. Because the produce stays firm in the tray after labeling, the label is always visible on each individual crop.
Up to 500 patterns can be programmed into Sinclair’s new Compact Pattern Labeller (CPL) system, which the company introduced in 2017, Lawson says. “You pick the pattern that you want to run, and then you do not have to crank the cassettes, or the heads, to go up and down, according to the size of fruit,” he says. “It’s already loaded according to the pattern that you have.”
With Sinclair’s multiple systems, the company aims for integration and smart technology, allowing packers to walk around with tablets and know their labeling percentage, and be aware of when they will run out of cassettes. “They want early warning systems, so to speak, so they want diagnostics,” Lawson says.
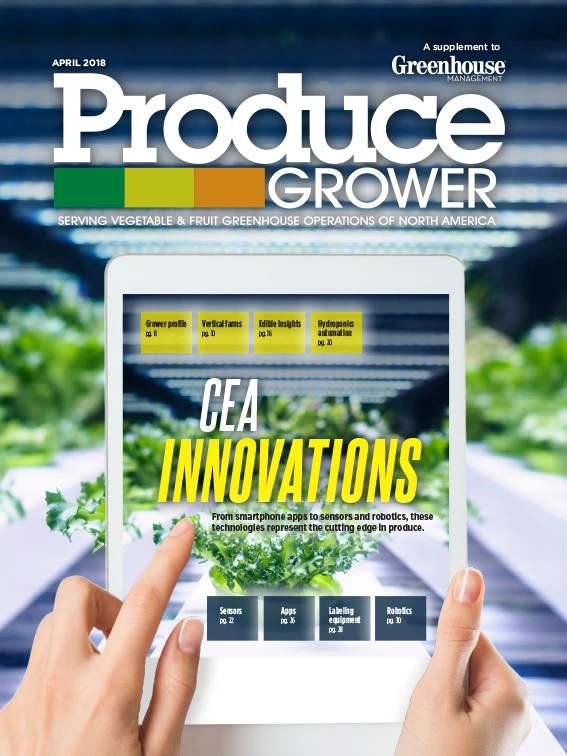
Explore the April 2018 Issue
Check out more from this issue and find your next story to read.
Latest from Produce Grower
- University of Evansville launches 'We Grow Aces!' to tackle food insecurity with anu, eko Solutions
- Lawsuit challenges new H-2 visa rules
- Q&A: Sandra Eskin Leads Food Safety Advocacy Organization, STOP, as CEO
- Find out what's in FMI's Power of Produce 2025 report
- The Growth Industry Episode 3: Across the Pond with Neville Stein
- Martin A. Makary Sworn in as FDA Commissioner
- PG CEA HERB Part 2: Analyzing basil nutrient disorders
- LettUs Grow, KG Systems partner on Advanced Aeroponics technology