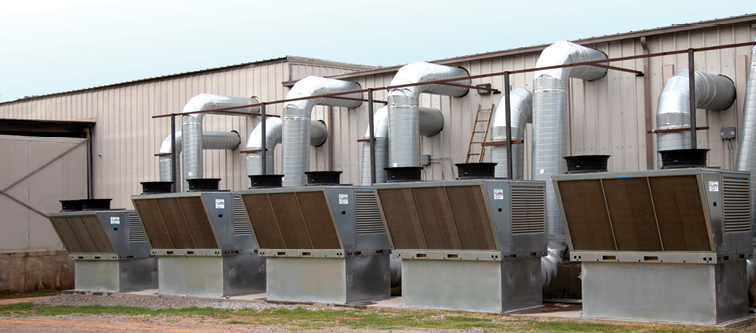
Whether it’s a mechanically cooled greenhouse, a sealed hybrid facility or an indoor vertical farm, a controlled environment agriculture (CEA) operation’s success hinges on finding the right balance among technology, ecology and the specific needs of cultivated crops.
There is arguably no system more important to that balance than the HVAC system. Whether or not these systems have integrated dehumidification, commissioning HVAC units is critical to a facility’s launch and its ongoing upkeep.
The Department of Energy’s Office of Energy Efficiency & Renewable Energy defines commissioning (Cx) as the process verifying “whether a building is performing according to its original design and intent and meets the needs of its owners and occupants. This quality-assurance process helps to identify deficiencies that could lead to equipment failure, increased energy use, and poor indoor air quality so that building operators can better maintain their facilities.”
Commissioning HVAC systems tailored to CEA’s unique demands tests system capabilities to identify issues and establish a baseline, as well as enables the fine-tuning of settings for different crop varieties.
Every aspect of this process plays a vital role in ensuring both the initial success and long-term sustainability of CEA operations. Additionally, commissioned HVAC systems can unlock energy savings of up to 40%, according to Jan Westra, strategic business developer at RII member Priva.
This article is an overview of the key aspects and easily overlooked areas of commissioning CEA HVAC systems, from pre-plant introduction checks to ongoing commissioning once the facility is fully operational. For a step-by-step guide, download RII’s HVAC Best Practices Guide at bit.ly/RII-HVAC.
Pre-plant commissioning
CEA facility operators should commission their HVAC systems before introducing plants into the environment to establish an equipment baseline and catch any drastic issues that would lead to catastrophic crop outcomes.
“Whenever something fails, you’d rather have it fail when there are no plants around than when you’re already in production. You cannot afford so many errors in that case,” Westra says.
Ideally, a third-party commissioning agent will be conducting these activities to bring a fresh and unbiased perspective to the review process. The Cx agent will need access to equipment specification documentation (manufacturer specs for motors, pumps, energy systems, etc.), as well as to the original design plans and building specifications to help establish the baseline performance and identify any design issues.
Westra suggests working from the smallest pieces of equipment back to the larger systems and controllers. “It starts with checking if the sensors are connected to the right connection,” he says.
In highly automated facilities, there could be hundreds of sensors that affect HVAC performance and efficiency, including EC, pH, CO2, temperature, relative humidity, anemometer (wind speed) and PAR/light sensors.
Another item to check before plants are introduced to the environment is piping to ensure everything is flowing in the right direction. An HVAC system that accidentally dumps cold air instead of warm air into the growing environment because two fittings are swapped could wreak havoc on your crop and energy loads.
During an RII-hosted webinar on commissioning CEA facilities, Mike Zartarian of RII member organization Zartarian Engineering stressed the importance of having dedicated experts conduct systems commissioning.
“It’s not really a reasonable ask to have the grower responsible for all the technical stuff that goes into checking out this system that’s never worked to find if it’s going to work,” he said. “Commissioning is happening at the same time the grower is trying to hire a team. They’re thinking about plant schedules; a lot of times they are fairly recently hired. We find it truly helpful to have separate folks who are focusing on the technical nitty-gritty leading up to that and checking from the plant’s perspective that everything is going to go well and then hand the grower a working system.”
Post-plant commissioning
The Cx process continues once plants are introduced to the cultivation environments. Plants add an incredible amount of heat and moisture load to the spaces they occupy, so it is important to ensure that the HVAC system can still operate as designed and as efficiently as possible with those added loads. These tests and verifications can take two weeks, depending on facility size, equipment used and integration sophistication.
Once the HVAC system and its components have been checked against design plans and controls have been programmed, performance testing can commence.
As noted in RII’s HVAC Best Practices Guide, “functional performance testing of HVAC systems and their associated controls allows […] commissioning agents to run equipment through its paces to ensure it responds as designed and check that system alarms are connected and enabled as expected.”
During functional testing, Cx agents can simulate different cultivation space conditions by manipulating environmental control systems to observe how motors activate and how systems respond to maintain target settings.
The HVAC Working Group behind the HVAC Best Practices Guide recommends “ensuring HVAC systems manage temperature and humidity when actual environmental conditions in cultivation spaces are outside of target ranges, observing how climate control systems respond to significant changes in HVAC loads (such as when lighting systems are turned on and off), and verifying that day-night temperature differential can be achieved in various scenarios.” This can be done during the pre-plant Cx stage but will need to be completed again once the plants are added.
When commissioning an HVAC system with plants in the cultivation environment, operators will need to pay close attention to sensor placement, as rooms can have variations of several degrees. For example, a sensor placed on the outside edge of the canopy near a heating vent “[can make you have] a 3° Celsius difference in what you punch in versus what is going to show up right at the plant level,” Zartarian says.
Ensuring sensors are placed throughout the room and at plant canopy height will enable tighter control over the environment and avoid plant stress.
Josh Gerovac, another speaker during the webinar and founder of the consultancy Symbiescent Crop Advisor, advises operators to pay close attention to lights-on and lights-off events, saying, “Right as the lights kick off, you’re going to have a humidity spike…that you need to deal with. If you don’t have some supplemental dehumidification or a gas reheat or electric reheat setup on your HVAC equipment…you’re going to run into problems.”
Continuous commissioning
Commissioning a CEA HVAC system is not a one-and-done affair — it’s a continuous process that occurs at regular intervals in your facility’s development. Ideally, every CEA operation should aim to commission its HVAC system (and its facility as a whole) at least once a year. “In the build environment, we call that continuous commissioning,” Westra says.
Continuous commissioning can help identify when equipment falls out of specified performance ranges due to maintenance needs, or when humans intervene with equipment and leave without reconfiguring it according to standard operating procedures (SOPs).
For example, a service tech could manually override a faulty heat pump that didn’t start on schedule over the winter holidays to prevent a crop failure but forget to investigate further after the holiday break.
“And then it stays that way the rest of the year,” Westra describes. “So all summer long, the warm water heat pump valve is open. The system tries to send an off signal toward the pump, but there’s an override and the pump keeps on running.”
An SOP as simple as leaving a cabinet door open to indicate the equipment behind was manually set to on or off instead of left on “auto” (i.e. controller-operated) could help avoid these oversights. Westra also advises that facility operators pay close attention to hard-to-reach areas or zones obstructed by plants or large equipment, as that’s where corners are often cut.
Continuous commissioning also aims to optimize system performance through improved automation and better-tuned controls. Centralizing controls within a sophisticated system can enable facility operators to dial in HVAC, irrigation, lighting, airflow and fertigation for increased resource efficiency and plant health, as well as reduced systems and plant stress.
Taking this approach one step further, fine-tuning these controls for each plant growth stage can maximize benefits.
“Growing plants considers all the plant components: roots, shoots and fruits. Ignoring these connections leads to sub-optimization,” Westra says. “If all aspects are taken into account, not only is optimization possible, it leads to optimal solutions and more autonomy in model-based controls.”
At the end of every Cx project, CEA operators will be left with a report outlining any repairs needed or operations that can be fine-tuned for optimized efficiency.
If new processes or equipment are introduced because of a Cx project, those reports potentially can be used to unlock rebates through energy efficiency programs.
As CEA operations evolve and efficiency standards change, ongoing commissioning becomes a cornerstone for maintaining peak performance and identifying areas for improvement.
Get curated news on YOUR industry.
Enter your email to receive our newsletters.
Explore the August 2024 Issue
Check out more from this issue and find your next story to read.
Latest from Produce Grower
- PG CEA HERB Part 2: Analyzing basil nutrient disorders
- University of Evansville launches 'We Grow Aces!' to tackle food insecurity with anu, eko Solutions
- LettUs Grow, KG Systems partner on Advanced Aeroponics technology
- Find out what's in FMI's Power of Produce 2025 report
- The Growth Industry Episode 3: Across the Pond with Neville Stein
- The Growth Industry Episode 2: Emily Showalter on how Willoway Nurseries transformed its business
- 80 Acres Farms expands to Georgia, Texas and Colorado
- How BrightFarms quadrupled capacity in six months