

According to Justin Bartlett, the CFO of Legacy Labor, the biggest misconception growers have about H-2A labor is understanding exactly what it is.
“A lot of people start doing research and see how many rules and regulations they need to follow that they get overwhelmed,” Bartlett says. “There are agents out there that can file paperwork for you, get workers approved, all of that — even recruit for you and get them to your farm. But once they show up on your farm, they are your employees. And all of the compliance falls on you as a grower.”
That’s where H-2A companies like Legacy can step in. Legacy takes on compliance responsibilities for its clients, handling all of the necessary applications and paperwork so growers don’t have to. Labor compaies like Legacy handle the HR component too. That means growers can focus on what matters most: growing high-quality produce.
“The risk and exposure as a company with the Department of Labor (DOL), for fines — that’s the biggest thing,” Bartlett says. “You can’t put a number on that. DOL could show up and give you a six-figure fine pretty quickly on certain things. There’s still some exposure [if you have someone else handle it], but it’s very minimal. The day-to-day worker management for H-2A — hiring, firing, disciplinary, payroll — all of that falls on us or another company that provides this service if you go that route. It’s a really big job for an HR person to not just manage the workers, but keep track of all of the rules and changes.”

While H-2A labor comes with costs, Bartlett says it’s best to think of it as an investment in the business. With increased labor, that means there are more hands on deck to expand production or improve efficiency in growing. With the needed workers — and Legacy can help determine how many workers a grower needs — any gaps in production can be filled.
One of their clients, greenhouse grass grower Hoffman Nursery, specifically needed H-2A to combat what it called a “labor lull” in its area. By using H-2A labor, they were able to increase productivity, increase product quality by paying more attention to detail, and remove any unknowns when it came to its workforce.
It went so well, in fact, that they increased their number of workers from year one to year two.
“That speaks for itself,” Bartlett says.
WANT MORE?
Enter your email to receive our newsletters.
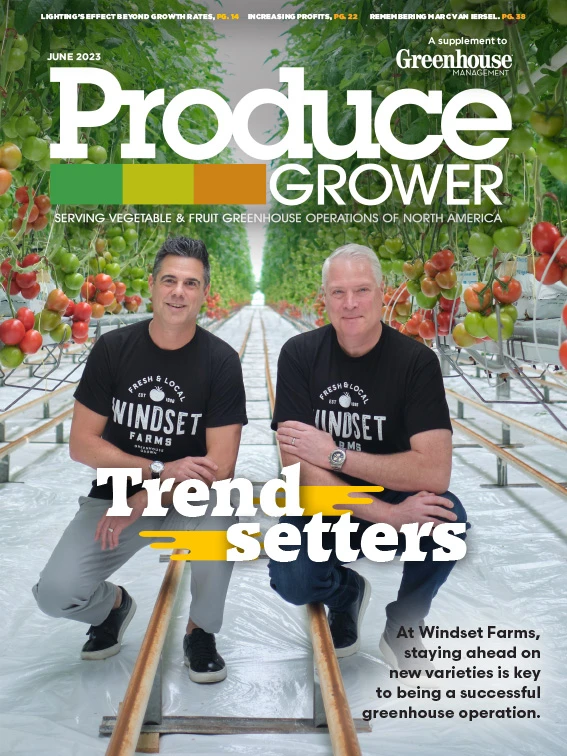
Explore the June 2023 Issue
Check out more from this issue and find your next story to read.
Latest from Produce Grower
- University of Evansville launches 'We Grow Aces!' to tackle food insecurity with anu, eko Solutions
- LettUs Grow, KG Systems partner on Advanced Aeroponics technology
- Find out what's in FMI's Power of Produce 2025 report
- The Growth Industry Episode 3: Across the Pond with Neville Stein
- The Growth Industry Episode 2: Emily Showalter on how Willoway Nurseries transformed its business
- How BrightFarms quadrupled capacity in six months
- Oasis Grower Solutions releases two foam AeroSubstrates for hydroponic growers
- FDA Intends to Extend Compliance Date for Food Traceability Rule