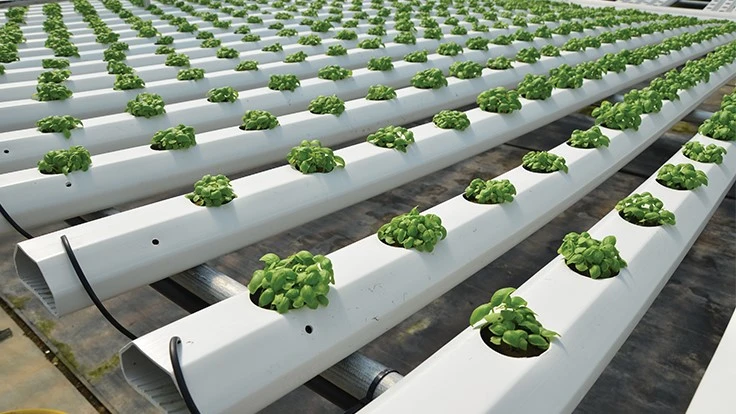

A cornerstone environmental parameter is light. The energy cost of heating a greenhouse transmitting “free” sunlight is often less than the energy costs incurred by sole-source lighting for indoor production. However, recent advances and increased efficacy of LED fixtures have made sole-source lighting and indoor production more feasible for certain types of production.
Why would anyone want to produce specialty crops indoors, void of natural sunlight? One reason may be extreme or seasonal weather conditions. Although we consider greenhouses to be controlled environments, it is often impossible to have consistent temperatures and light levels throughout the year. This in turn makes year-round production of food crops challenging. Indoor plant factories and vertical farms can be more precisely controlled, especially for difficult to grow crops (ie. tissue-culture transplants) and to improve uniformity and plant quality, and to reduce losses. High-value young plant production can be moved indoors for the same reasons.


Though young plants such as plugs can be successfully produced in the greenhouse as they have been for many years, moving production indoors can allow for more precise environmental control. Through this, we can potentially reduce crop times, increase uniformity, improve quality and reduce shrink. These seem like goals we should have for our entire production, right?
With the more expensive capital and operating costs for indoor production, high-value and high-density crops may be the best place to start. For example, you may produce 200 plugs in a flat in the same area that five to 20 finished plants can be grown. If the higher cost can be spread across a larger number of plants, the cost per plant is less.
Now to address one of the largest indoor production operational expenses: lighting. The quantity, quality and duration of light a plant receives plays a large role in the yield, development and morphology of that plant. With supplemental and sole-source lighting becoming increasingly popular and the increased efficacy and reduced cost of LEDs, growers can decide at what stage of growth to provide extra light and at what intensity. The quantity of light a plant receives can be manipulated through both intensity and photoperiod.
In this article, we will discuss intensity. If light intensities are too low, plants may become leggy, remain very small, have poor root systems or grow poorly once transplanted into their final production environment, whether that is a greenhouse or outdoors. However, if the light intensity is too high, the plants may not be using the light efficiently and you waste energy. The light may also cause leaf damage and reduce growth and plant quality.

Experimental protocol
If we provide increased inputs (such as higher light intensities during indoor production) throughout the seedling stage, can we increase growth? If so, can these more robust transplants result in increased yields at harvest? These are some of the questions we set out to answer in this study.
We grew basil because it is one of the most popular fresh culinary herbs grown in controlled environments. ‘Nufar’ seeds were sown in Grodan rock-wool cubes and placed under Fluence Ray 66 PhysioSpec Indoor LED fixtures in a walk-in growth room. The fixtures provided broad spectrum white light with light ratios (%) of 19:39:39:3 blue:green:red:far-red and target light intensities of 100, 200, 400 and 600 µmol·m–2·s–1 (Fig. 1). Lights were on for 16 hours to create daily light integrals (DLIs) of 6, 12, 23 or 35 mol·m?2·d?1. After two weeks under the different light intensity treatments, the seedlings were transplanted into deep flow technique (DFT) hydroponic systems in a common greenhouse environment. They were grown at an average daily temperature of 73 °F (23 °C) and a DLI of 14 mol·m?2·d?1 for three weeks after which they were harvested. With the plants growing in a common environment, we could evaluate whether the inputs at the seedling stage influenced growth, morphology and yield at harvest.

Results
At cotyledon emergence, it was visually apparent that there were differences between the light intensity treatments as seedlings germinated under 600 µmol·m–2·s–1 had larger cotyledons than those germinated under 100 µmol·m–2·s–1, however, we did not quantify this (Fig. 2). At transplant, two weeks after sowing, the fresh weight of basil seedlings grown under 600 µmol·m–2·s–1 was 287% greater than those grown under 100 µmol·m–2·s–1 and the leaf area was 738% greater (Fig. 3 and 4). Though this great of a difference in weight and leaf area is exciting, it is only the seedlings and is not directly an indicator of finished production yields and profits.
After three weeks of growing in the greenhouse, there were visual differences between the seedling light intensity treatments (Fig. 5). For example, the number of branches increased as indoor light intensity increased up to 400 µmol·m–2·s–1 with those grown under 100 µmol·m–2·s–1 having 2 fewer branches, than those plants grown under 400 or 600 µmol·m–2·s–1. The fresh weight at harvest also increased as seedling light intensity increased. For example, plants grown under 100, 200, 400 and 600 µmol·m–2·s–1 weighed an average of 32, 39, 54 and 58 g, respectively, at harvest. That is an 80% increase in fresh mass yield between plants grown under 100 and 600 µmol·m–2·s–1.

Take-home message
Although light intensities of 400 to 600 µmol·m–2·s–1 are above what most indoor facilities currently provide, we have shown that these intensities during basil seedling production can have a large impact on harvestable yield. Though results may be species dependent, we are currently conducting studies on other species to provide more complete recommendations (stay tuned for more information). Also, different production times or growing multiple seeds per cell may alter the results. We always recommend conducting your own trials before widespread adoption.

Explore the June 2019 Issue
Check out more from this issue and find your next story to read.
Latest from Produce Grower
- The Growth Industry Episode 3: Across the Pond with Neville Stein
- PG CEA HERB Part 2: Analyzing basil nutrient disorders
- University of Evansville launches 'We Grow Aces!' to tackle food insecurity with anu, eko Solutions
- LettUs Grow, KG Systems partner on Advanced Aeroponics technology
- Find out what's in FMI's Power of Produce 2025 report
- The Growth Industry Episode 2: Emily Showalter on how Willoway Nurseries transformed its business
- 80 Acres Farms expands to Georgia, Texas and Colorado
- How BrightFarms quadrupled capacity in six months