
Aiming to resolve labor shortages and improve space efficiency at greenhouse operations producing leafy greens, Green Automation develops, manufactures and sells automated growing systems with movable gutters for nutrient film technique (NFT) hydroponic lettuce production. The company is based in Finland and established a U.S.-based subsidiary, Green Automation Americas, in 2015. Its North American clients include Little Leaf Farms in Devens, Massachusetts; lef Farms in Loudon, New Hampshire; and Gotham Greens in New York City and Chicago.
“Our system is more like a manufacturing production system in some ways,” says Green Automation Americas CEO Patrik Borenius. “It [can have] hundreds of conveyor belts and thousands of sensors. Everything’s automated. You almost need a different skillset. You need factory people more so than [greenhouse] labor, and you have very few people,” he says.
Green Automation’s technology includes gutters that automatically adjust to separate crops as they grow, Borenius says. The systems give plants enough space to grow, while at the same time trying to ensure as much space efficiency as possible in the greenhouse.

The systems
The company has tiers of automation from system to system, Borenius says. Green Automation’s Automated System, which is optimized for head lettuce production, requires humans to perform certain tasks, such as transplanting seedlings into the growing system and harvesting. “In the beginning, everything’s very close together,” Borenius says. “That’s really where the efficiency comes from, having everything really close together when [the plants] don’t need the space. Only as they grow, that’s when — up to five stages, over the length of the greenhouse — those gutters separate out from each other, until the final spacing, which could be seven, eight inches apart for those gutters, for the heads to give them the space they need.”
By comparison, Green Automation’s Fully Automated System is optimized for baby leaf lettuce production and doesn’t involve any human contact with the produce, Borenius says. “The seeding is [done directly] into the gutter, then germination takes place in the system,” he says. “Then at the end of the growing cycle, those gutters are moved on turntables and conveyors to an automatic cutting machine [to harvest the lettuce]. The substrate is removed automatically, the gutters are cleaned, and then it starts again — the process with the automatic filling step, either rockwool or peat — and then seeding again.”
Out of Green Automation America’s clients, lef Farms and Little Leaf Farms produce baby leaf lettuce using the Fully Automated System, while Gotham Greens uses the Automated Growing System to produce head lettuce and herbs. Because Gotham Greens grows its product in rooftop greenhouses and has some dimension restrictions within its houses, the company has incorporated more manual steps into its process.
In addition to offering technology, Green Automation Americas has an advantage over European technology companies that work in the produce space, Borenius says. “We’re selling the systems in U.S. dollars from a U.S. entity to a client,” he says. “You don’t have to deal with exchange rates — Euros.”

Founded in Finland
Green Automation’s founders, Tero Rapila and Juhana Kantola, are from Finland. For more than 40 years, Rapila’s family has run a lettuce greenhouse operation. “Initially, they developed a system for their own use, and they did this back in the ’80s,” he says. “They started out and improved it further and further, and the system got better and better. Then in 2002, they decided to go out into the market and sell this to other growers around the world.”
Rapila and Kantola created the technology because manual greenhouse production involves many labor-intensive steps, but there was a scarcity of labor in Finland and a high cost associated with it. Finland imported fresh lettuce from Spain, Greece and Portugal, and the product lost its freshness and nutritional value during long deliveries.
“It’s like a six-day truck trip — very expensive,” says Borenius, who was born to Finnish parents in Germany and now lives in the United States. “[The founders] very early realized that we really need to do this ourselves. It’s very difficult to get it from all the way down in Spain, so they started with this.”
Because of its climate, Finland has a short growing season, so Rapila and Kantola realized greenhouse production would be the best way to provide consumers with fresh and locally grown produce, Borenius says. Decades later, the technology that addressed labor problems in Northern Europe in the 1980s began to help growers facing similar issues in North America.

Competing with megatrends
Borenius sees many agricultural “megatrends” impacting agricultural open-field operations in the Western United States. Many of these operations use an abundance of water, which is in scarce supply, and unsustainable amounts of nitrate from many of their fertilizer programs enter aquifers. Meanwhile, field growers are encountering more trouble finding labor; while extreme, unpredictable weather hurts their yields. Borenius has noticed demand increasing for pesticide-free hydroponic greenhouse production, and he thinks it can be cost-competitive with open-field growers if greenhouse producers address space and labor efficiency, as well as energy efficiency.
Green Automation recommends growers produce in greenhouses and use light from the sun for energy efficiency, but the company could arrange its growing system in layers for vertical farm or plant factory applications, Borenius says. “There will always be the need to be as space-efficient as possible, to minimize the investment, optimize it, and there will always be a need to be as labor-efficient as possible, because whatever happens in the future, labor will be an issue,” he says.
“You’ve got to get the highest yields per square foot in your greenhouse, and then you’ve got to do it with as little labor as possible,” Borenius says. “We think our system is absolutely a key component of achieving this, at least for leafy greens. There are other systems for other crops that make sense, but for leafy greens, we think we’re really on the forefront of this.”
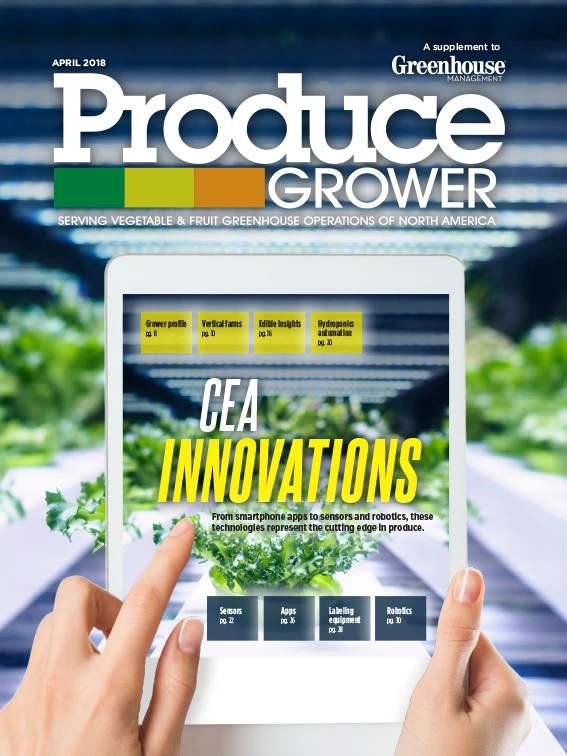
Explore the April 2018 Issue
Check out more from this issue and find your next story to read.
Latest from Produce Grower
- University of Evansville launches 'We Grow Aces!' to tackle food insecurity with anu, eko Solutions
- Lawsuit challenges new H-2 visa rules
- Q&A: Sandra Eskin Leads Food Safety Advocacy Organization, STOP, as CEO
- Find out what's in FMI's Power of Produce 2025 report
- The Growth Industry Episode 3: Across the Pond with Neville Stein
- Martin A. Makary Sworn in as FDA Commissioner
- PG CEA HERB Part 2: Analyzing basil nutrient disorders
- LettUs Grow, KG Systems partner on Advanced Aeroponics technology