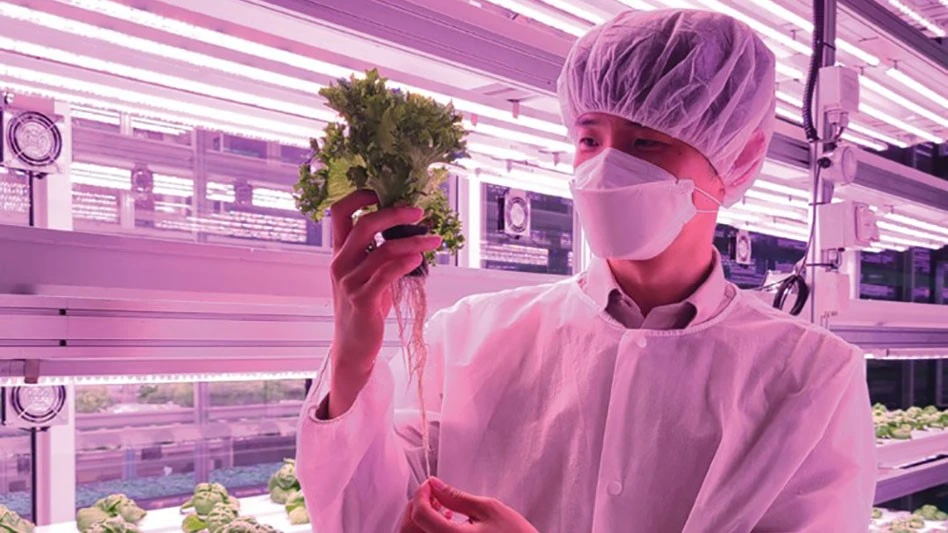

Michael Evans, director and professor at the Controlled Environment Agriculture School of Plant and Environmental Sciences, Virginia Tech
The state of Virginia has a rich agricultural history. This past year, that history modernized with AeroFarms expanding its facility in Pittsville County and Plenty announcing plans to build a $300 million vertical farming campus in Chesterfield County.
That isn’t lost on Michael Evans, the director and a professor at the Controlled Environment Agriculture School of Plant and Environmental Sciences at Virginia Tech University. He says the school is working on various projects, ranging from vertical farming research to breeding genetics for CEA to more traditional hydroponic growing. The throughline, Evans says, is approaching CEA with the idea of challenging themselves by partnering with companies and researchers that would push boundaries. Part of that, he says, is working with the private sector to push CEA to new levels, but also to help bring businesses to the state.
“We have a very high level of interactive partnering research activities going on with private sector entities,” Evans says. “And because of IALR's [Institute for Advanced Learning and Research] mission doing economic development in our state, we’ve built ourselves around that as well, by helping the state recruit and support CEA companies.”
Asked if he was surprised that CEA has attracted so much investment, Evans says he was not and notes that, even inside Virginia Tech, it’s not uncommon for his department to work with another college (say, the engineering college) on a CEA project.
“You’ve probably noticed this as you look at a lot of companies,” he says. “There are a lot of entrepreneurs and people driving this that may not have originally been even in horticulture to begin with. This is an area that has brought in a lot of non-traditional horticulture or greenhouse type people into it.”
“Those folks can often see things in different ways from the way that people like me see it having been in it for a long time. They often bring a new energy, new visions, new ideas. They aren’t boxed in and that creates a lot of really exciting ideas and energy. ... The other thing is that CEA always has been, and probably always will be, driven by technology. Improvements in LEDs, for example, have made indoor vertical farming possible. But technology is really a driver in this field. We look at, and as we work with companies, there are so many companies that see CEA and may have technologies that aren’t market ready or have that were developed for other uses in other markets, but might be really useful in CEA and need expertise to help them bring it over. That’s where we feel like we are really useful at partnering with the private sector.”

Ryan Dickson, professor and researcher, University of Arkansas
At the University of Arkansas, professor and extension specialist Ryan Dickson is working on a number of different projects. One is a collaboration for vertical farming leader Bowery Farming on developing spinach cultivars designed for CEA.
“We’re looking at resistance to Pythium for spinach,” Dickson says. “That’s in collaboration with Bowery. It’s looking promising. ... We’re basically screening selections of spinach to see if there’s any tolerance to Pythium and if different disease complexes matter in hydroponic systems.”
One other project Dickson is spearheading is growing blackberries indoors. Below, he explains the parameters of the project, how the technology is trickling over from Europe and why it’s a project he loves working on:
“We, at the University of Arkansas, have a world-renowned blackberry breeding program. We’ve teamed up with the plant breeders here and the extension faculty. My niche, my added value is working on growing blackberries in soilless substrates, mostly using long cane techniques. It can take several different shapes, but long cane is the generic term. It’s a technique that’s come out of Europe — it’s been used for decades for raspberries, as well as blackberries. The technology and that interest is just starting to filter over to North America.
“If you’re familiar with some work that Chieri Kubota has done with soilless strawberry production, this is similar. She started that 10 or so years ago in the U.S. and it’s grown. That’s now the main crop we think of in terms of soilless greenhouse production. Raspberries and blackberries are next in line. We’re probably where strawberries were a couple of years ago, but the potential for growth is what’s on everybody’s mind. We’re doing some cultivar screenings looking at yield, crop timing, tracking the amount of heat units that need to go into blackberries in order to get them to flower and fruit. We’ve put together a prototype of a crop scheduling tool so a grower could say ‘OK, this is the blackberry or raspberry cultivar that I want to grow. I’ve got this dormant plant. And if I put it at this temperature, it will take this amount of time to flower and harvest.’ It’s very similar to the early temperature and climate modeling work that’s been done in floriculture crops over the past couple of decades.
“It’s incredibly exciting [to be working on this]. It’s one of my favorite projects because it’s so new. It’s almost too new in some respects, but we are definitely one of the early adopters on the research front and the growers getting involved now are early adopters as well. As a researcher, doing something that no one has done before and helping an emerging industry evolve and grow is incredibly exciting to me. That’s our charge - to see if we can make as much progress as we can as quickly as possible so that we can make an impact and be recognized in this area.”


Marc van Iersel, professor and researcher, University of Georgia
Marc van Iersel has been working with greenhouse lighting for the past decade. While, according to him, greenhouse lighting research has “always really been focused on the plants and how to grow them,” van Iersel is starting to ask other questions, like “How does greenhouse lighting fit into the overall utility grid? How can we make sure that we don’t generate a lot more strain on the utility grid?”
“That is a problem in many places where we’re just limited by the size of the infrastructure that we have to move electricity around. And so, if the greenhouse industry can find ways to shift its electricity use away from the times that other industries or consumers are using a lot of electricity, then we can reduce that peak demand on the overall utility network. That is something that utility companies are really interested in, and I think that utility companies are going to be very willing to provide incentives to greenhouses to make sure that that load is shifted away from peak hours.
“A lot of utility companies are providing incentives to replace high pressure sodium lights with LEDs just to reduce overall power usage. We are now starting to see some utility companies that are starting to provide incentives for installing smart lighting control systems that can either reduce power use or that can shift their power use away from peak hours. So the utility companies are definitely putting money on the table to get this implemented right now on the controller side, I think. Those rebates are still relatively rare, but we will see a lot more of that in the near future.
“In Ontario, where there are a lot of greenhouses, and pretty much all with supplemental lighting, they’re literally running out of power, out of electricity. Not because they cannot generate more electricity, but because they cannot get it to the Niagara Peninsula. They don’t have the transmission lines to get more power to that part of Canada. And so we can imagine how important it would be for the utility companies there to smooth out that overall electricity demand. So it’s about shifting the greenhouse electricity to times of day that nobody else is using a lot of electricity. So, can we do more lighting at night, for example?”
After testing out the automated smart lighting systems he’s been working on at UGA, van Iersel and his team are ready to put it to the test on a larger scale in a commercial greenhouse.
“What we want to do next is go into a commercial greenhouse and try this on a much bigger scale and track how the crops in that greenhouse respond to those kinds of changes and see if the crops still grow just as well and see what kind of practical issues we run into when we go to a commercial greenhouse.
“We have one tentative partner, James Greenhouse, that’s close to Athens. They are an ornamental propagator … and they produce a lot of cuttings as well. We hope to be able to get started there in the middle of January. We want to get this going. And the goal is to go through the winter and early spring of 2024. We need to see how the crop responds to it, so we don’t want to do that in just a few weeks.”
Beyond greenhouse lighting, van Iersel’s lab is also working on using multispectral imaging to take pictures of crops and detect nutrient deficiencies and pathogens.
“Multispectral imaging just refers to taking pictures basically on the different colors of light and then taking pictures of the crop and then analyzing those images. We get all kinds of information out of it. Traditionally, that has been a tool that is used quite a bit in research, but it has been really expensive, so about five years ago, we actually bought one of these commercial multispectral imaging systems and it was a little bit over $40,000, I believe. And then we looked at what that system was actually doing and we kind of laughed and said, well, that’s simple. And we’ve since built our own version of it — and we’re not engineers — but we could build that kind of an imaging system for $500. We reduced the cost by about 99%. So, if we can do that, obviously a qualified engineer can do it even better. So, I’m convinced that people will start seeing this kind of technology in greenhouses before too long.
“And there are at least some pathogens that we can detect. We haven’t tried very many, but I think there is real potential here. So, what I would envision for the future is that you would have one or more of these systems in the greenhouse, and it would likely move through the greenhouse at night when there’s no sunlight to interfere with the images. It takes pictures, stitches them all together and analyzes them for you, so when you come into the greenhouse in the morning, a report is waiting for you that advises you to check this part of the greenhouse because it may have some problems here or there.
“And at some point, hopefully these systems would be able to at least tentatively identify the problem. But I think even if it can just tell you that there is something that doesn’t look right at a very early stage, the hope is that you can catch problems earlier than what you can do by just looking with your own eyes. Because the reality is that a camera is more sensitive than our eyes. If you can find problems really early, then hopefully you can mitigate those problems before they spin out of control. And we’re not there yet, but we’re working to show that there’s potential to do this. At some point, I’m sure that commercial companies will jump in and start developing systems that that will be well suited for commercial greenhouses, and hopefully not charge $40,000 for it. So, we are going to publish exactly how you can build your own system. But what we have is too bulky and too clumsy to put in a greenhouse and move it around. As I always like to say, that’s just an engineering problem. I know that’s an issue that can be addressed by the right people that aren’t me. But I have no doubt that will happen.”

Chieri Kubota, professor and researcher, Ohio State University
Chieri Kubota at Ohio State University has her plate full with several different research projects, including growing leafy greens in low-pH solutions as a form of pest control.
“One of the projects is a new way to grow hydroponic leafy greens. What we have worked over the past five years is trying to grow leafy greens in a much lower pH, so in an acidic nutrient solution. Usually you don’t do that, but we want to try that because an acidic nutrient solution can potentially protect plants from disease. It’s like how, with pickles, for example, you can store fresh produce for a long time because it’s an acidic solution. Making the produce more acidic can protect it from fungal disease and stuff like that. So, we are reducing pH to a crazy low like 4 or 4.5. The typical pH range is 5.5 to 6.5, so going down to 4 or 4.5 is a very unusual approach, but we found that many crop species can tolerate that range.”
“And then our plant pathology study with my collaborator in the plant pathology department also confirmed that some of the fungal disease in hydroponics can’t tolerate low pH, so we are about to start recommending a low pH approach as a sort of preventative method for leafy greens because this is one of the big issues for leafy greens. If you encounter pythium or other diseases, then you have to basically terminate the production because it’s very difficult to control. So that’s one interesting project.”
Kubota, who introduced greenhouse strawberry production to the United States more than a decade ago, is bolstering her research to include propagation. She is also working on using different lighting and airflow strategies to mitigate tipburn in lettuce in vertical farms, and she is working on vegetable transplant technology called vegetable grafting.

Explore the December 2022 Issue
Check out more from this issue and find your next story to read.
Latest from Produce Grower
- Consumer Curiosity Report explores food, nutrition opinions from 'early adopters'
- Your comprehensive guide to Indoor Ag-Con ’25
- Sollum Technologies and Indoor Ag-Con announce recipients of Sollum Student Scholarship
- 80 Acres Farms expands to Georgia, Texas and Colorado
- This fast and agile robotic insect could someday aid in mechanical pollination
- AmericanHort urges exclusion of sphagnum peat moss from proposed Canadian tariff
- The Growth Industry Episode 2: Emily Showalter on how Willoway Nurseries transformed its business
- Moleaer expands irrigation product line featuring nanobubble technology